高强度低合金钢,填充焊丝表面涂层的开发,对焊缝金属的影响
高强度低合金钢主要是通过铁水预处理、转炉精炼等多步冶金新技术和控轧控冷轧制方法得到,具有超洁净度、超均匀性和超细晶粒组织的特点。低合金钢是在碳素钢的基础上添加一定量的合金化元素而成。
其合金元素的质量分数一般不超过5%,用以提高钢的强度并保证其具有一定的塑性和韧性,或使钢具有某些特殊性能,如耐低温、耐高温或耐腐蚀等。常用来制作焊接结构的低合金钢可分为高强度钢、低温用钢、耐腐蚀用钢及珠光体耐热钢四种。
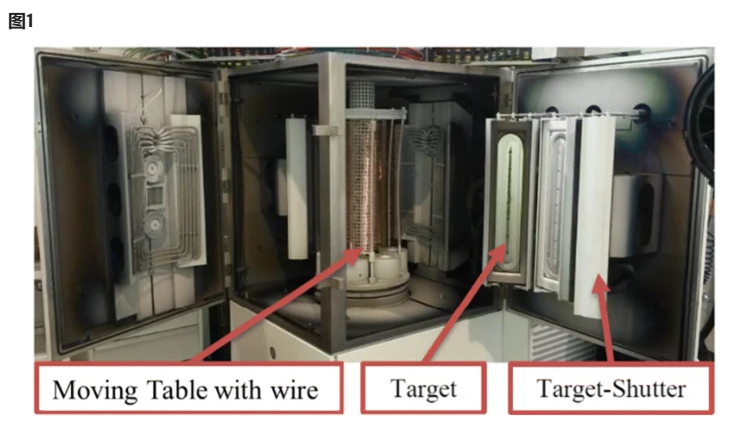
低合金高强钢具有良好的焊接性、优良的可成形性及较低的制造成本,因此被广泛用于压力容器、车辆、桥梁、建筑、工程机械、矿山机械、纺织机械、海洋结构等领域。随着现代工业的发展,在焊接结构方面都趋向大型化,大容量和高参数的方向发展,在焊接低合金高强钢的生产出现了许多新的问题,其中较为普遍而又十分严重的就是焊接裂纹。
常见的焊接裂纹根据生成时的温度,可分成热裂纹、冷裂纹和再热裂纹等几类。在焊接低中合金高强钢最容易出现的是冷裂纹。冷裂纹是指焊接接头冷却到较低温度时所产生的裂纹。冷裂纹包括:延迟裂纹、淬硬裂纹、低塑性脆化裂纹等,正常所说的冷裂纹指的是延迟裂纹。
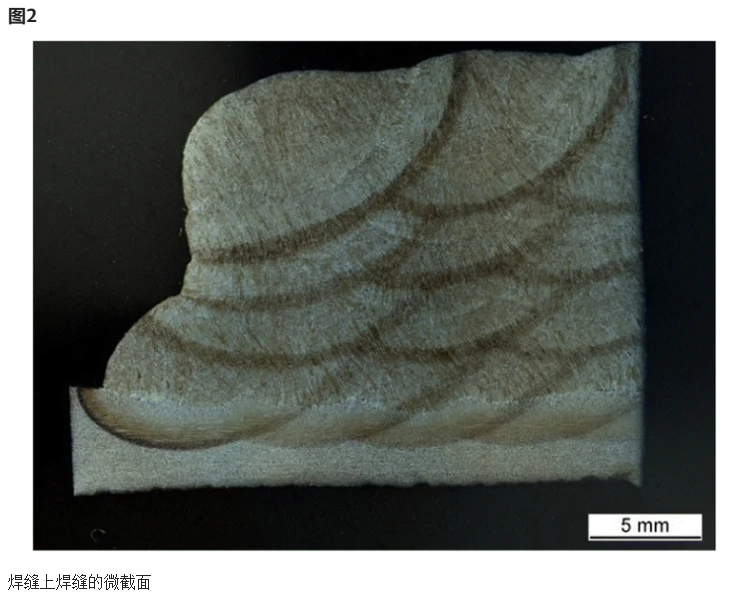
钢结构的轻质结构通常受到焊接金属机械性能的限制。现代母材的强度值在焊缝金属中无法实现。非常需要开发焊接材料,以便在不限制其潜力的情况下加工现代细晶粒结构钢。焊丝的物理气相沉积(PVD)涂层可将Mn4Ni2CrMo焊丝焊条的焊缝金属强度提高多达30%。
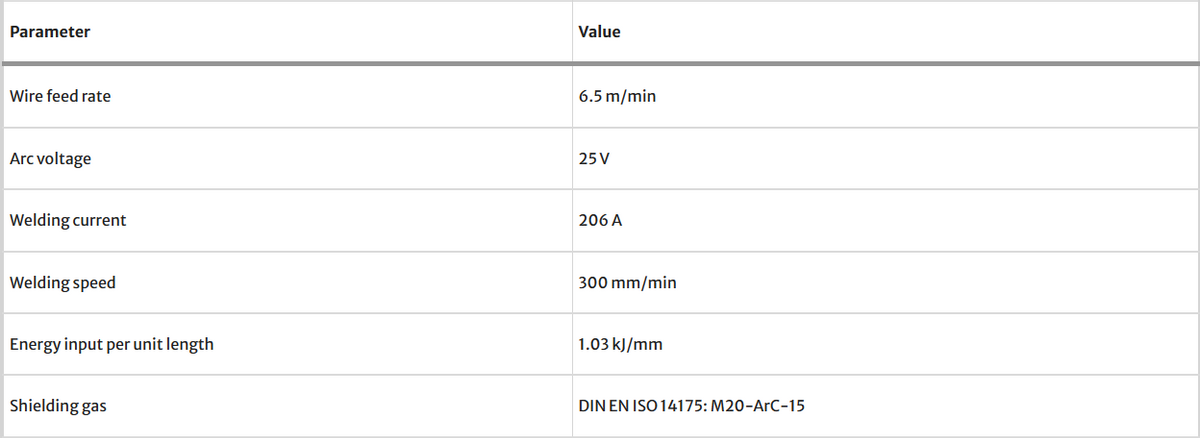
通过使用不同的涂层元件,可以利用霍尔-佩奇关系,并实现强度的提高。特别是通过应用钛、钒和钇涂层,可以提高焊缝金属的强度。由于涂层的多层结构,焊缝金属和工艺可以相互独立地受到影响。讨论了单元素涂层和多组分涂层对焊缝金属和工艺的影响。PVD涂层允许焊丝电极根据要求进行个性化调整。
建筑和工业设备工程不断增长的需求可以通过轻质结构来满足。这一研究领域的钢铁开发正在向前推进,特别是为了减少自重和提高承载能力。现代细晶粒结构钢的屈服强度达到1300 MPa,从而减少了材料使用。
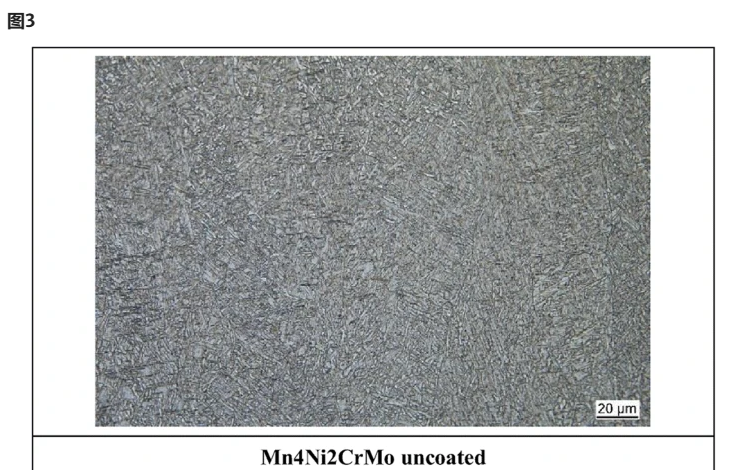
高强度钢的强度增加主要通过晶粒细化来实现,并基于霍尔-佩奇关系。因此,不同合金元素对焊缝金属、晶粒尺寸和结晶的影响在高强度钢研究中具有很高的兴趣。铌已被证明是一种特别适合晶粒细化的元素。除铌外,钛等其他元素也适用于影响焊缝金属。
使用这些钢时的限制因素是焊接金属中可以实现的强度。母材的强度无法在焊缝金属中达到与目前可用的填充金属,因此有必要开发合适的焊丝电极。物理气相沉积(PVD)涂层工艺使薄层能够应用于焊丝电极。所得的电极丝可用于加工所述的钢种。质量为Mn4Ni2CrMo的电极丝可用作基板。

通过改变不同元素的施加层厚度,可以研究焊缝金属相对于层元素的不同质量分数的机械性能。除了单元素涂层外,焊缝金属的性能还可能受到几种涂层元素(多组分和多层涂层)的适应性组合的影响。
最先进的技术是调整焊丝电极的合金化,以便在焊接金属中获得更高的强度。这是可能的,因为尽管延展性有限,拉丝工艺本身仍然是可能的。对焊缝金属强度产生深远影响的另一种方法是使用药芯焊丝,尽管与实心焊丝相比,氢含量有所增加。
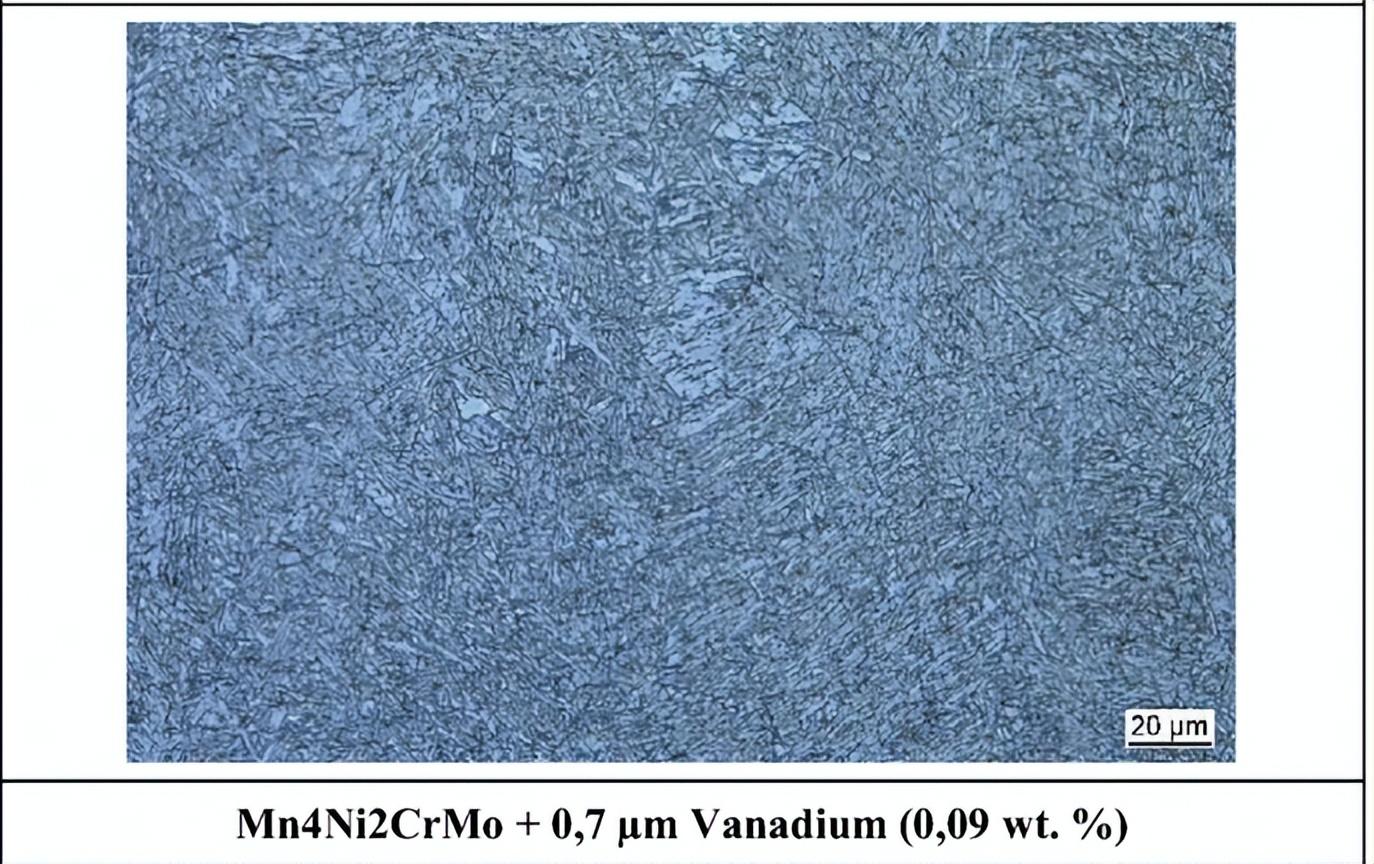
涂层焊丝方法扩展了焊缝金属成分可能受到影响的范围,而不受拉丝工艺的限制或药芯焊条的氢问题。图显示了Cemecon CC-800/9定制涂层系统的涂层室,该系统用于根据工业标准涂覆PVD涂层。材料在真空室中汽化,并在基材(焊丝)上凝结成薄层。因此,工艺气体(氩气)通过施加的电压电离。氩离子沿涂层材料(目标)的方向加速并蒸发。汽化材料被引导通过电场并撞击要涂覆的部件。
用于所述研究的基板材料是直径为4.2mm的合金Mn1Ni2CrMo的GMAW线电极。电极丝分批送入系统并涂覆。为此,它被缠绕在腔室中的载体结构上。为了确定各自的总涂层厚度,在每个过程中都涂覆了一个额外的样品。涂层厚度是在卡洛特研磨的基础上确定的。在多层涂层的情况下,确定总涂层厚度。

将焊丝焊接在基板上以确定焊丝电极的机械性能。几个并排的焊缝和几层相互重叠的焊缝(板焊缝)如图2所示施加的焊缝金属长度为200毫米,宽度为60毫米,高约15毫米。将基板预热至100°,各个焊缝之间也保持100°C的层间温度。焊丝以这种方式焊接,以便从焊缝金属中取出大量样品。即使与DIN EN ISO 15792-1的程序相比,强度损失是预期的,因此选择了该程序,因为测试的重点是没有稀释的纯焊缝金属。
图2显示了多层焊接盲缝的微截面,从中采集了用于确定焊缝金属机械性能的样品。按照DIN EN ISO 6892在焊缝的纵向上采集拉伸试样,横向采集符合DIN EN ISO 148-1 的夏比冲击试验试样。此外,还采集了显微切片样品和显微照片。

为了可视化不同涂层元素对焊缝金属结构的影响,对试样进行了抛光并用酒精硝酸(Nital)蚀刻。图3显示了涂层焊丝电极与未涂覆参比焊丝电极(Mn4Ni2CrMo)的焊接金属对比。除了涂层厚度外,还给出了计算出的质量分数。可以清楚地看到,钇、钒和钛涂层增加了针状铁素体在微观结构中的比例,这最初表明屈服强度更高。此外,由于涂层,晶粒细化。
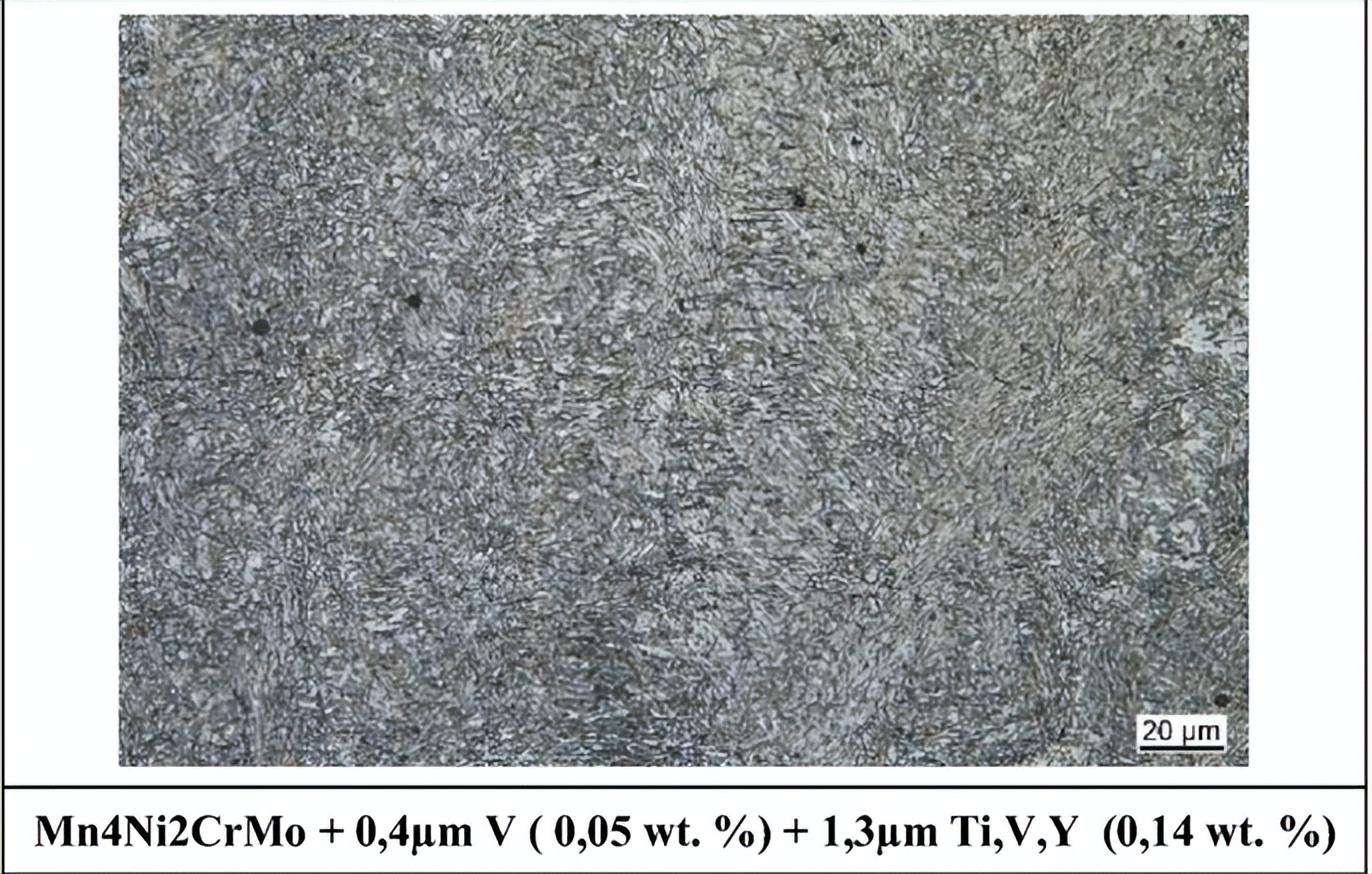
除了单个涂层元素外,还测试了由多种元素组成的涂层的影响。为此,在影响矩阵中评估了单元素涂层对焊缝金属的影响。为了进一步提高强度,开发了多组分和多层涂层,它们由测试的各个组件组成。涂有钛、钒和钇元素(多组分涂层)的焊丝电极的焊丝金属的微观结构如图所示。涂层厚度达到1.3μm。图4还显示了焊丝电极的结构,焊丝电极上沉积了0.4μm厚的钒层,顶部沉积了第二层钛钒和钇,因此总层厚度为1.7μm。同样在这里,给定的质量分数是计算值。
具有纯钒涂层的电极在加工过程中显示出更多的飞溅,焊缝质量相应较差。为了利用由于钒含量增加而显着增加的强度,同时以工艺稳定的方式加工电极,在彼此之上施加了几层(多层涂层)。为了更详细地检查焊缝金属结构,拍摄了SEM图像,如图5所示可见马氏体显微组织。
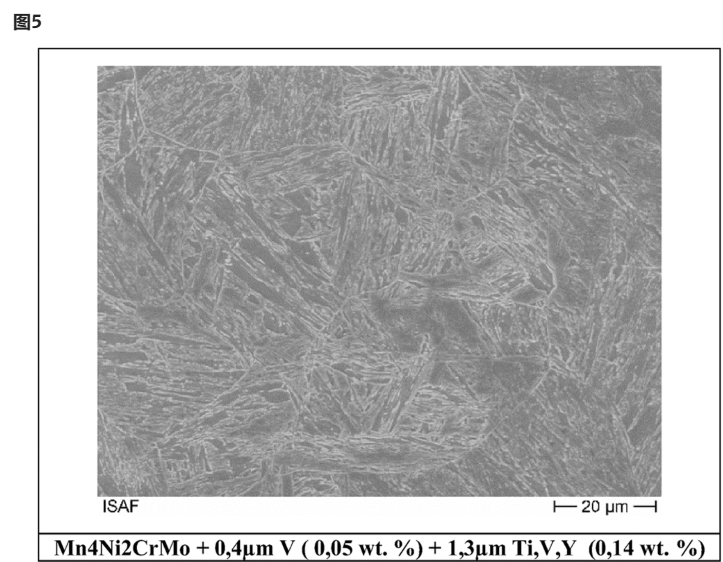
描述材料从涂层到焊接金属过渡的研究仍在进行中。不同位置的显微照片表明对微观结构的影响是均匀的。进行了电感耦合等离子体-光学发射光谱法(ICP-OES)以证明材料从涂层到焊缝金属的转移。表显示了包括涂层元件在内的各种焊缝金属的化学成分。
可以清楚地看到,与参考焊缝金属相比,可以通过涂覆涂层来增加相应的元素含量。但是,确定的值低于计算的质量分数,这是由于电弧燃烧造成的。Ti涂层焊丝电极焊缝金属中的钒含量高于V涂层焊丝焊缝金属中的钒含量。关于V型涂层和燃烧对电弧影响的研究仍在进行中。
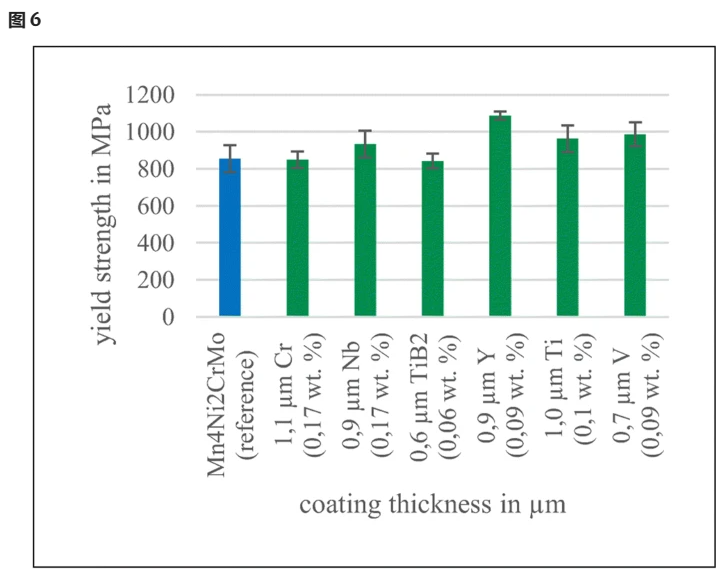
还通过进行ICP-OES分析研究了多组分涂层和多层涂层的转变。表3显示了多组分涂层和多层涂层的化学成分。在这里,还可以验证涂层元件向焊缝金属的转变。总结了各种涂层元素对焊缝金属屈服强度的影响。
涂层元素钛、钒和钇导致焊缝金属屈服强度显着提高。通过溅射0.9μm钇涂层,屈服强度可以从855MPa提高到1087MPa,从而提高27%。这一增加代表了单个涂层元素测试中的最大值。钒和钛也显著提高了屈服强度。使用钛涂层,屈服强度可以以可重复的方式提高13%。钒涂层将屈服强度提高了15%。
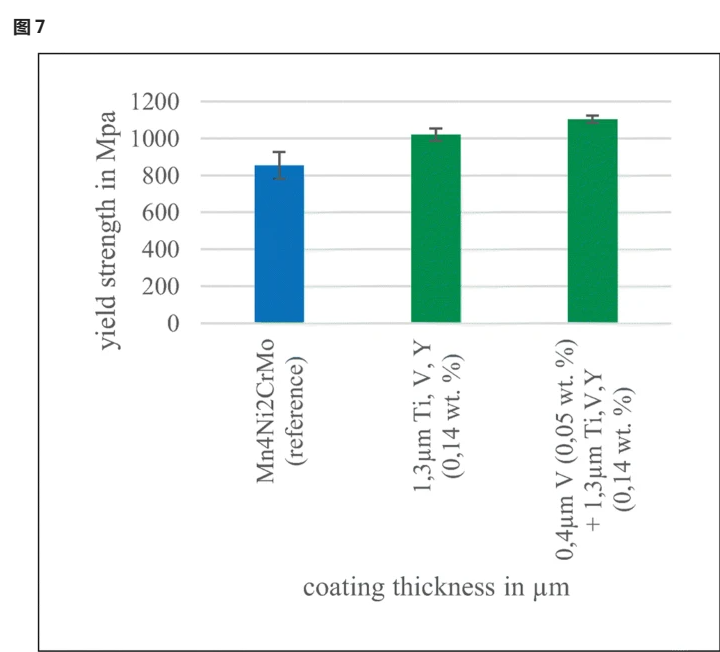
图7比较了图4所示的微观结构和合金成分的强度。用参照焊缝金属。与参比电极相比,具有多组分涂层的电极强度仅提高了30%。相比之下,带有附加钒涂层(多层系统)的电极可实现强度提高以及体现多组分涂层和多层涂层对屈服强度的影响,表4显示了与相应涂层相关的屈服强度、拉伸强度和断裂伸长率。实验在室温下进行。
此外,在加工涂层焊条时,焊缝金属的延展性也会受到影响。与未涂覆的参比线电极相比,涂覆的电极在室温下显示出显着较低的冲击能量。与现有技术相比,在测试中实现的可重复屈服强度代表了显着的进一步发展。焊丝涂层不仅影响焊缝金属的性能,还影响焊接过程的性能。
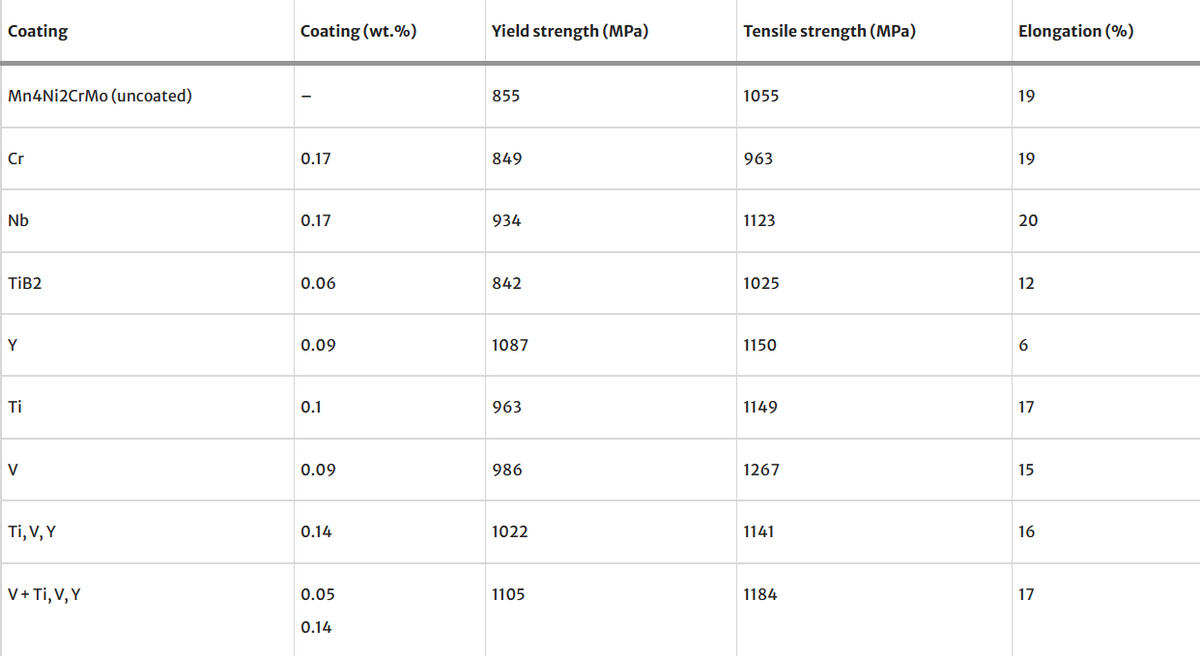
制作了电弧的高速视频来分析焊接过程。此外,在焊接过程中测量电流和电压,从而记录焊接的能耗。图8显示了焊接过程中电流和电压的曲线。比较焊缝的能量吸收处于同一水平。在电弧中蒸发的涂层元件会导致电弧等离子体的变化。等离子体的变化导致弧的变化和弧长的透视。这在电弧的高速图像中很明显。
低合金高强钢中w(C)一般控制在0.20%以下,为了确保钢的强度和韧性,通过添加适量的Mn、Mo 等合金元素及 V、Nb、Ti、A1、等微合金化元素,配合适当的轧制工艺或热处理工艺来保证钢材具有优良的综合力学性能。
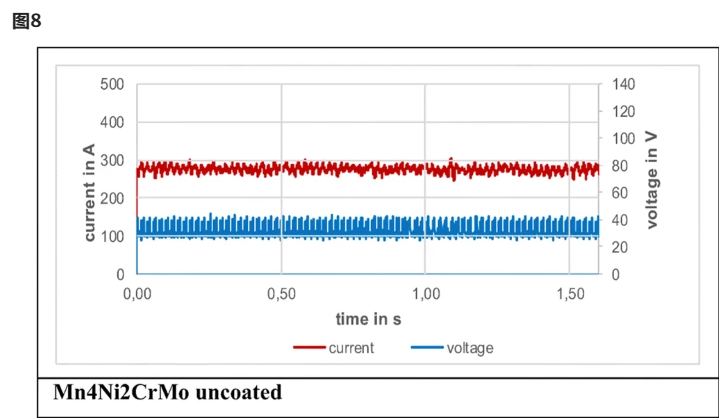
由于低合金高强度钢具有良好的焊接性、优良的可成形性及较低的制造成本,因此。被广泛地用于压力容器、车辆、桥梁、建筑、机械、海洋结构、船舶等制造中,已成为大型焊接结构中最主要的结构材料之一。
低合金高强钢的强化机理与碳素钢不同,碳素钢主要通过钢中的碳含量形成珠光体、贝氏体和马氏体来达到强化;而低合金高强钢的强化主要是通过品粒细化、沉淀硬化及亚结构的变化来实现。
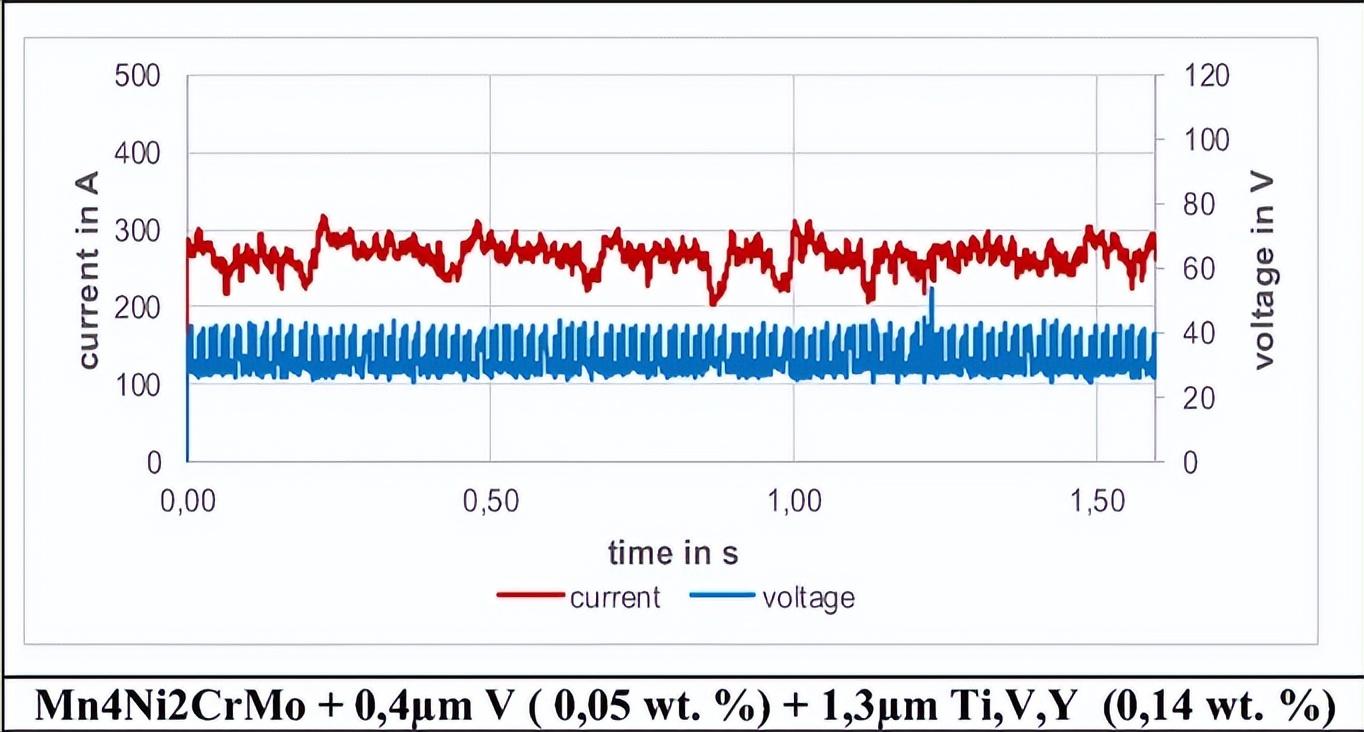
通过在PVD工艺中涂覆GMAW焊丝,可以在很大程度上影响焊缝金属结构以及焊缝金属强度。特别是,可以将晶粒细化元素引入焊缝金属中。通过涂层系统,焊接金属的强度最多可提高30%。多层涂层提供了几乎分别调整焊接金属强度和焊接工艺的可能性。
如果将晶粒细化和强度增加元素用作外层,它们也会对加工性能产生负面影响。这些可以用工艺稳定的涂层元件覆盖。通过Mn4Ni2CrMo焊丝焊条涂层,可以在1105 J的冲击能量下实现37 MPa的可重复平均屈服强度。这代表了对当前研究状态的重大进步。